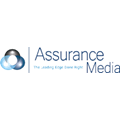
Featured Project Return to Projects List
Commercial Call Center
Project Information
- Project Location:
- Newark, DE
- Status:
- Completed - Jul 2019
- Structure Type:
- Office Building
References
- General Contractor:
- Nickle Electric
Scope Of Work
Background
Sometime in January 2019, Nickle Electric contacted Assurance Media to provide an estimate for the telecommunications infrastructure in a client's new Newark hub office and regional call center. The client was pricing out different locations for a large-scale consolidation of their Delaware call centers. The initial estimate was budgetary. The design was completed and Assurance Media was selected for the opportunity to complete the job, but the timeline for construction was the most aggressive that our company has seen in this our 10th year in business. The client needed to have people working in the space by mid-July, approximately 6 months from the initial phone call. Usually, projects of this scale take 1 to two years from planning to completion. Our team was up for the challenge, even though the spring and summer seasons are our busiest time of the year. Because the design specifications we were given were for budgetary consideration initially, we were missing a lot of key details of the client's company-wide facility specification. As the client provided these specifications, we were effectively telling them what they could afford based on their budget and with long lead times for specialty materials. We ordered what we could get immediately, and our poor warehouse team had a huge challenge in finding space to store miles and miles of specialty cable in our warehouse during our busy season.
The Project
Completing the job in 4 months required some outside-of-the-box planning. The design called for 2,790 data cables for workstations and phones as well as another 250 cables for audiovisual solutions provided by another contractor. 16 data racks in 7 telecom closets and a central distribution frame on the ground floor. To provide added value, our team worked directly with the cable manufacturer for special pricing and expedited delivery of the components needed. We were able to discount approximately $100,000 in materials by partnering directly with the manufacturer. Our team staged materials at our warehouse by floor and wing of the building so they could load up at our shop by the pallet and effectively form bucket brigades of material delivery right to where it was needed on the job site. Our project management team utilized more cost-effective temporary labor for this task whenever possible, leaving our full-time team to concentrate on the highly specialized tasks of connecting a large-scale network. The majority of the work occurred within 5 weeks and it was all hands-on deck. Our scheduling team changed the monthly scheduling meeting to daily for 2 months during this project to find additional resources to use from elsewhere in the company. The entire company was put on alert and anyone who finished any job early on any day over the span of the project knew they were needed on that job site. Components were bundled by workstation and dropped off in advance of our team actively working on them. Teammates came over to help after their other jobs were finished for the day. They would simply arrive and begin on a row with components ready for them. Our team utilized a new method of large-scale quality control on this project. We were spread thin by this project across our entire book of business, and our top foremen and PMs would work on their respective projects until their regular workdays were completed and then would head over to the call center job site. There they would inspect the exceptionally speedy work of the core project team and correct or change any work outside the customer specification. We staggered the schedules of these high-level technicians such that overtime hours were spread out evenly among the team to mitigate costs and give our guys a break. It was not uncommon for any given Assurance Media technician to have a workweek with days off during the week and night shifts or weekends on for QC and cable pulling or termination work. On multiple occasions, our leadership and office admin teams would head over to the job site with Chick-Fil-A or pizza and feed the troops working there outside on picnic benches. 30 of our 47 technicians spent time working on the call center project.
There were multiple revisions to the design of the network, some were well communicated by other contractors and some were not. This was due to the overall renovation’s scale and speed. On multiple occasions our team would cable an entire wall of connections and then upon returning the next day would find the wall no longer there and the cables bundled up in the ceiling or cut completely. They would ask around and learn the wall was edited out the night before, after our team left. When these drastic and sweeping changes would happen, all contractors would be working on these areas simultaneously causing our team to have to wait or communicate well with our fellow contractors to work at the same time. Our team cabled a conference room and tested all cables to completion to be told 3 days later that that conference room was becoming more workstation space or a café. Our team persevered, they were exhausted from working as fast as they could and would be forced backward and pushed ahead to catch back up to the aggressive pace. The stylish and accommodating motorized Sit/Stand desks the client used for their employees were not designed with cable management in mind at all. The long rows of desks did not have pass-throughs from desk to desk and our team had to fish each cable in and out of each desk frame to get to the next. The jacks in the desks had to be oriented upside down and backward on the back of the frame to be accessible for patch cables to devices. The wood facades of the desks made the data jacks very difficult to reach and secure, and our team also had to consider space for the power cables that would come with the devices at the workstations. Floating drop ceiling sections that were installed made challenges for floor core drilled pathways holding large bundles of cable for the floor above.
The client's employees began arriving on-site for work before we were finished working. Our team would stagger efforts between sections of the building to get them ready for occupants and keep our team out of the way of their regular workdays. In a beautiful display of teamwork with the client's IT and engineers, our team was performing testing and final checks in teams of 2, followed by a team of 2 to 3 customer IT Technicians who were assembling the computers and monitors on desks and connecting them to the network for the first day of use in the morning.