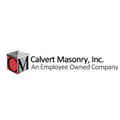
Calvert Masonry, Inc.
Manassas, VA 20109
Featured Project Return to Projects List
Waterfront at Southwest
Project Information
- Project Location:
- Washington, DC
- Status:
- Completed
- Structure Type:
- Mixed Use
References
- General Contractor:
- Clark Construction
Scope Of Work
Waterfront Southwest consists of twin eight (8) story office buildings with retail level, located adjacent to the Arena Stage and the Maine Avenue marina and marketplace. A terra cotta rain screen cladding system has been implemented primarily on the North and East elevations of both buildings. While rain screen systems have extensively been in use in Europe since the 1980’s, it is relatively new to the United States and specifically the Mid-Atlantic region.
This project is the largest Terra Cotta rain screen project to date in the metropolitan Washington, DC area. The terra cotta cladding system consists of 1-9/16 inch thick ceramic clay tile panels on the exterior face, with air space and mineral wool cavity insulation between the panels and building substrate. Overlapping horizontal joints between panels prevent driving rain from entering the cavity, yet allow air flow upward within the cavity to assist in keeping the cavity free of trapped moisture and heat. Panels are locked into place with retaining clips and pressure gaskets, and the panel weight and wind load are transferred to the building structure by an engineered aluminum support system. The terra cotta panels offer a long life and low maintenance building skin that can be provided in a variety of high quality natural colors and finishes, as well as in glazed finishes for high exposure areas.
The Waterfront project incorporates over 11,000 each through body terra cotta panels from the 2nd floor up, consisting of eleven (11) inch nominal height flat panels of three separate colors, and a ribbed panel profile of a fourth color. These panels are installed in up to five (5) foot lengths, with the colors located in a specified location and pattern throughout the façade. In addition, over 1,500 each glazed terra cotta panels are installed below the 2nd floor and consist of:
• 11-inch high in glazed colors corresponding to the three flat panel colors above – this provides these façade areas with superior cleaning characteristics at the street/sidewalk area
• 8-inch nominal high glazed panels, in nine (9) distinct colors installed in specified location and pattern, located at the retail areas.
The aluminum support system required a high degree of layout and coordination with substrate and opening systems already installed ahead of our work, to insure proper spacing and alignments for vertical joints in up to 70 feet of continuous run, and horizontal joints up to 125 feet of continuous run. Adjustment in the two piece support system to account for substrate tolerances in and out was also required, and our crews expended considerable effort to insure that support system installation would accommodate the tight production tolerances and large sizes of the terra cotta panels. Over 16,000 lineal feet of horizontal aluminum framing, and over 13,000 feet of vertical framing, were installed on the project.
There were many challenges to the terra cotta system installation:
• Over two thirds of the terra cotta elevations commenced from a 2nd or 3rd floor roof/terrace deck, requiring materials to first be lifted from the ground to those deck locations, then raised from the deck level to the scaffold work elevations. FRACO mast climbing scaffold units were utilized on the project, with crane arms installed to lift the materials to the scaffold level. Slabs at scaffold tower locations were post shored below where required.
• A Henry Blueskin air/vapor system was selected and installed on the project, and incorporated a foil skin covering for UV resistance during construction. The foil skin application made locating of the light gage substrate framing very difficult for our crews during the installation of the aluminum support system. A detailed procedure for locating subframing and the sealing of penetrations into the air barrier was developed with the collaboration of the General Contractor, Clark Construction Group, the air barrier contractor and Calvert Masonry, in consultation with the designer (Shalom Baranes Associates) and the Owner’s skin consultant.
• The building envelope design includes several window openings with small terra cotta clad piers (side to side) and spandrels (head below to sill above) between. Unlike conventional masonry construction, in which the masonry is constructed in advance of window and trim installation, all window systems and trim were installed prior to terra cotta system installation start. In spite of best efforts to hold tight tolerances during the light gage, sheathing and window system installations, there were variances in vertical and horizontal alignments that our crews had to overcome to achieve consistent joint lines between panels. Modification procedures for metal framing, clip and panel adjustments were developed in conjunction with the system designer, represented by Shildan, Inc., and implemented.
• Extensive coordination, site inventory/consolidation and logistics planning was required resulting from the four separate through body colors and twelve different glazed tile colors, each being produced in several sizes to match predetermined joint and mullion layouts. Over 350 separate and unique tile piece marks were created for production, packaging, shipping and installation purposes to account for the different combinations of colors, lengths and locations.