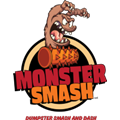
Monster Smash
Coraopolis, PA 15108
Metal Recycling Company
By: Monster Smash
October 2021
Case Study:
Metal recycling company with dumpsters located at their customer’s facility for acquiring metal scrap.
Customer Description:
A regional scrap metal processing company of ferrous and non-ferrous metals in the recycling industry.
Challenge:
Improving the efficiencies and cost reduction regarding company switching out of dumpsters at their client’s location.
- Waste Material – Light but large metal products, such as aluminum and aluminum alloys, for the heating and air conditioning (HVAC) industry.
- Method of Disposal – Customer forklifts tumble large, old air conditioning units into a metal dumpster creating extreme gaps between the units.
- Assessment – Over 70% of the overall container consists of air rather than material at the time when the dumpster encounters safety height restrictions, whereby no additional material can be added.
Problems:
- Safety – For their client, excess of waste material accumulates throughout the facility creating unsafe conditions.
- Unproductive Time - Time is wasted by their client’s employees to rehandle the material waste, thus resulting in increasing costs and decreasing production.
- Weight – Because the air conditioning units are large, space is consumed quickly, however, the weight of the overall dumpster is light.
- Costly Methodology - Once the height levels are capped, the recycling company is obligated to pick up the dumpster, however, it is not profitable, because they rely on heavier weighted metals within their business model.
- Costly Outsourced Drivers – The recycling company relies on outsourced staffing to pick up / haul their dumpsters. When the outsourced driver experiences an overflow of waste above the mandated height levels, the driver must decline the pick-up but will still charge the recycling company for a “dry run.”
- Customer Service Decline – The company’s client is regularly upset with their work site being cluttered due to overflow of material, as well as the unreliability and untimely pick-up service of the hauler.
Implemented Action:
- Provided our smashing-service at the metal company’s client’s facility to gain additional space in the dumpster, as well as cleaned-up their facility of excess metal debris littered throughout the yard.
Results:
- 3-to-1 Compacting Ratio - The effectiveness of our smashing allotted material of three dumpsters to now be compacted into one dumpster.
- Savings – The metals company reduced their hauling costs by 66% and eliminated dry-run costs.
- Profit Increase - The metals company had heavier loads returned resulting in more revenue potential.
- Safety – The metals company’s client was no longer concerned about their facility experiencing excess waste material throughout their yard that posed a danger. They now have a cleaner facility.
- General Liability – The metals company’s client reduced the amount of haulers entering and leaving the facility, thus reducing their overall traffic.
- Increase Customer Service - Waste material is minimally handled by employees thus reducing the cost of production while increasing production.
- Environmental Liability Concerns – Because the metal material is located in the dumpster, both companies are less concerned about run-offs that could negatively impact the environment where it could drain in a nearby river.