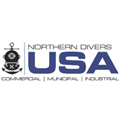
"Flush With Success"
A Deep-Water Lake Michigan Water Plant Intake Gets an Innovative Cleaning
An innovative high-velocity pipe cleaning system saves millions of dollars for a small water treatment plant on Lake Michigan.
Appeared in print as "Flush With Success"
By Scottie Dayton
January 2019
How We Do It - Water
Operators at the Two Rivers (Wisconsin) Waterworks noticed flow restrictions in the 24-inch raw water intake pipe in Lake Michigan that limited production to 1.6 mgd, versus the water treatment plant’s 3 mgd design.
In late 2015, the Wisconsin Department of Natural Resources told the city to address the problem, which threatened the plant’s ability to meet emergency water demands. In May 2017, the city hired Hibbard Inshore of Auburn Hills, Michigan, to inspect the pipe using a SeaBotix LBV 600-6 MiniROV (Teledyne ISCO).
Divers saw layers of zebra mussels on the wooden crib across the intake riser. The 12 to 18 inches of sediment and mussel shells in the pipe was deep enough to mire the ROV after it advanced 9 feet. “The only solution was to replace the line, but our community of 11,000 couldn’t afford it,” says Ross Blaha, water utility director.
While visiting the Lake Forest (Illinois) Water Plant, Blaha noticed the name Northern Divers USA on the raw water intake pipe. “It was a stroke of luck,” he says. “Owner Frank Frosolone Sr. and his team had cleaned the line recently and saved the city millions of dollars. Like us, their water source is Lake Michigan.”
In late August 2017, Blaha and Greg Buckley, city manager, watched the divers implement the high-velocity cleaning system at the Glencoe Village (Illinois) Water Plant. “We were sold,” Blaha says. Two Rivers Waterworks became the first in the state to use the process, which successfully cleaned the intake pipe.
Planning ahead
Constructed in 1924, the cast iron raw water intake pipe runs 6,000 feet from a depth of 34 feet to the shorewell. Water flows by gravity, entering the structure through a 90-degree cast iron elbow connected to the drop pipe attached to the plant line. Operators maintain a depth of 15 feet in the 20-foot-diameter well.
The ultrafiltration facility feeds 12.5 percent sodium hypochlorite before finished water enters the plant’s high-lift pump station supplying two elevated storage reservoirs and a sealed reservoir serving a second pressure zone. “We store 3 million gallons, enough for 1.5 days,” Blaha says. “This project included a temporary water source and permanent piping in the well to facilitate future cleanings.”
Brian Hackman, P.E., BCEE, of Strand Associates, helped city officials obtain permits from the DNR and Army Corps of Engineers to work in the lake. Hackman calculated that cleaning the pipe equaled 5 percent of the cost to replace it. Improved hydraulics and less solids loading on the membrane filters would bring further savings.
Out with the old
Beginning in mid-July 2018, truckloads of equipment from a subcontractor began arriving. Foreman Tim Campbell, his assistant Erick Halaburt, and forklift driver Mark Bernal unloaded and staged it. “Cleaning the pipe took slightly longer than three days; preparing for it took 18 days,” Frosolone says.
Frosolone hired Hard Rock Concrete Cutters to core drill a 36-inch hole through six rows of bricks in the well wall for the 24-inch cleaning line. Removing the 90-degree elbow and 3 feet of drop pipe from the well required the entire Northern Divers USA team.
Diver Corey Gerenda attached suspension straps to the elbow, aided by Frank Frosolone Jr. topside, and Joe Villarreal, who monitored the communication cable and hoses supplying air to Gerenda’s dive helmet and hot water to his suit. (The water temperature was 54 degrees F.)
Frosolone Sr., controlling the Stellar 7630 crane on his truck, lowered the boom’s snatch block through a 36-by-48-inch hatch in the shorewell roof. With the straps attached to the block, the crane supported the elbow’s weight as Gerenda used an underwater torch to sever the nuts on the flange and cut through the drop pipe. Once the divers were out of the water, Villarreal communicated via radio with Frosolone as he “flew” the fitting out through the hatch with less than an inch clearance on all sides.
Sleds and elbows
Frosolone observes, “We use custom-fabricated 72- by 36- by 24-inch-deep sleds to help anchor the HDPE pipes in water, but welding on the 90-degree elbows happens on site based on the current pipe’s diameter.”
The team spent a day cutting 14-inch elbows with flanges to length, removing half the back of the elbows near the base and welding the fittings to the sleds. “The solid sled bottoms and elevated elbows eliminate drawing in sand and sediment,” Frosolone says.
“The elbows connect to 14-inch pipes running back to one of six pumps feeding the custom-built manifold. It sends flows up to 78,000 gpm at 10 feet per second through the intake pipe in the well. Out at the intake riser, water and material blast up like a volcanic eruption.”
Meanwhile, Campbell’s team moved the pumps and sleds into position along the shore, then began fusing pipe with a McElroy TracStar 900 Series 2 fusion machine. “We needed 150 feet of 12- and 24-inch pipe and six 150-foot lengths of 14-inch pipe,” he says.
Back at the shorewell, Frosolone faced another clearance problem as he lowered a 450-pound 24-inch HDPE DR 17 tee through the roof hatch. Diver Gerenda connected the tee inlet to the intake line and a tee outlet to the drop pipe. After placing a rubber gasket between the flanges, he secured them with 10 1.25-inch stainless steel threaded rods with nuts and washers.
Over several days, Frosolone’s crew connected two 45-degree elbows to the upper tee outlet, followed by a 90-degree elbow aligned with the hole in the wall. “The elbows had to swing out at an angle from the vertical to rest on the catwalk, enabling us to attach the suspension straps to the overhead hoist,” Frosolone says. Campbell and Halaburt helped manhandle the fittings until the flange holes aligned.
Out to sea
Frosolone put the first three pipe assemblies into the calm lake in early August. After Campbell and Halaburt attached a sled to a pipe via flanges, they secured a strap to the front of the pipe. Bernal slipped a lift fork through the loop in the strap, then raised and extended the boom 38 feet, pushing the assembly into the water.
Diver Gerenda swam the cable attached to the front of the sled to the pontoon dive boat offshore. Then he and diver Frosolone Jr. counteracted the force of the waves to help keep the floating pipe on course toward a red buoy.
Helmsman Frosolone Sr. communicated with Campbell via radio on how fast to pull as Bernal pushed the back of the pipe forward, guided by Halaburt’s hand signals. Campbell’s “all stop” signified that the rear pipe flange was aligned with the pump flange.
With the flange attachment completed, Frosolone tested the 12-inch temporary water supply pump and made a nasty discovery. “Spring storms had added 10 inches to the height of the sandbar, enabling a vortex to form at the sled,” he says. “To avoid sucking air, we had to push out the lines another 50 feet.”
A three-day wait for additional pipe gave the Mersino crew (Global Pump) time to undo the flange connections and drag the lines back on shore. Fusing the 50-foot sticks and setting all seven pipes in the lake took two days.
Turbulent waters
“Our start date was Aug. 13, and water industry people were coming from all over to watch,” Blaha says. In the August heat, Frosolone and Campbell’s people raced to connect the remaining piping.
On schedule, Frosolone flushed the temporary waterline and Campbell set the floats in the well at 10 and 15 feet. The pump, set on automatic, delivers up to 4 mgd. “That’s twice our summer demand,” Blaha says. “Even better, it didn’t increase our chlorine use.”
Not knowing where the pipe might be three-quarters blocked added to the challenge of cleaning it. “If I started too many pumps too soon, the velocity could cause a blockage or bulge the pipe,” Frosolone says. “Likewise, once the first pump starts, it can’t stop, or material will fall out of suspension and create a plug.”
With the dive boat stationed over the intake riser and the team’s ROV-1000 (Outland Technology) sending images to the surface, Frosolone started pump No. 1. The water, forced through the custom manifold under high volume and velocity, scoured the pipe without damaging it.
Villarreal sent the ROV images to Frosolone’s cellphone. Guided by how much debris spouted from the intake riser, he slowly started the remaining pumps. A brown plume soon stretched out for a mile, returning sediment to the lake.
Taming turbidity
The pumps ran nonstop for 80 hours, and Frosolone’s team monitored them on rotating 8-hour shifts. Every 12 hours, they sent down the ROV to check what was coming out of the riser. After they pumped 219 million gallons through the intake pipe, 100 percent clean water finally appeared.
“Previously, we couldn’t pump more than 1,000 gpm without seeing 10 NTU or higher,” Blaha says. “When we tested the pipe by increasing our flow to 1,600 gpm for 15 minutes, turbidity held at 0.90 NTU.”
Because the ROV wouldn’t fit in the pipe, Frosolone inspected it using a GoPro camera attached to his custom stabilization platform and a lift bag. “Frank Jr. went down with the apparatus, Ross increased the intake flow and the current dragged it in,” Frosolone says. “The inspection proved the line was clean.”
To prevent the short intake riser from sucking in lake-bottom debris, Frosolone fabricated a replacement: a 5-foot-high steel riser tapering from 6 to 2 feet square at the bottom. He also made a screen with a hatch for it. After towing the riser suspended by a lift bag into position, the divers bolted it to the intake flange.
“With the old riser and a strong southeast wind blowing over the lake, we’d see 15 NTU or greater,” Blaha says. “The highest turbidity we’ve seen with the new riser was 0.51 NTU, our average is 0.31 NTU and the low was 0.21 NTU. Those numbers are phenomenal.” Depending on lake action, Northern Divers USA will clean the intake pipe every three to five years.
Final detail
Storms or a rough lake often prevented offshore work. Frosolone used the time to clean the clogged 2-inch chlorine line using air pressure. The line terminated at the riser. “The air compressor ran for three days,” Blaha says. “We don’t know what was in the line because divers couldn’t grab a sample, but it’s open now. Frank saved the city $500,000 to replace it.”
When the weather cleared, Villarreal mounted a new chlorine feed line around the top of the riser to eliminate fittings and some piping. Additional feed points also dispense the chemical uniformly from all sides.