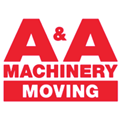
A & A Machinery Moving, Inc.
Morrisville, PA 19067
Featured Project Return to Projects List
Tissue Machine Dismantling
Project Information
- Project Location:
- Lincoln, ME
- Status:
- Completed - Oct 2016
- Structure Type:
- Manufacturing Plant
Scope Of Work
Scope of Work:
Disconnect, match-mark, dismantle and load a 2.5 meter Valmet Tissue Machine Mod. DCT100 from Lincoln Paper in Lincoln, ME, where it was installed new in 2006. All ancillary and support equipment such as burners, refiners, pumps and tanks were included in the relocation, along with large bore (>2” diameter) piping. A&A scope of work included all mechanical and electrical disconnects, dismantling, equipment cleaning and export crating and skidding. A&A was also responsible for coordinating transportation and heavy hauling provided by 3rd party through the owner.
Our unique approach to skidding/packaging included large skids up to 8’ W x 16’ L allowing packages of equipment with accompanying ancillary components to be grouped and shipped together and supported by detailed match-marking and photo logs. This enabled efficient just-in-time delivery from the staging warehouse to the project matching the reinstallation sequencing (reinstall by others).
Work was completed within schedule and with no extra costs above quoted price.
Project Details:
- 10 week, single-shift schedule
- 82 Truckloads – flats, vans, curtain-sides, containers
- Largest Piece – Yankee Dryer; 170,000#, 16’ diameter x 25’ long
- Fabricated custom shipping frame for Headbox
- Largest piece - Yankee Dryer ; 16’ diameter x 25’ long
- Roof section removal and restoration
- Match-marked original ISO’s; provided new ISO’s where missing
- Provided temporary building heat until rubber surfaced rolls removed
- Removed & shipped transformer at close of project
Unique Challenges:
Climate Control - During the initial dismantling phase which included building penetrations, we provided temporary heat to sustain a minimum ambient temperature around the machine until the rubber-coated rolls were removed and shipped in climate-controlled trailers.
Yankee Extraction - The 170,000# 16’ diameter Yankee Dryer was removed through the roof. Though a more costly extraction process than other approaches, this method was chosen because it represented the least schedule impact. Because the Yankee was located directly under a structural beam which could not be removed without significant engineering and additional building support, it was lifted and reset in an adjacent position allowing the rigging to be reset so the dryer could be lifted out clearing the overhead obstruction.
Schedule – the entire project including mobilization, clean-up, roof restoration and demobilization was required to be performed within a ten (10) week, single-shift period.