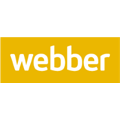
Featured Project Return to Projects List
City of Houston water plant
Project Information
- Project Location:
- Houston, TX
- Approx Contract:
- $200,000,000
- Status:
- Completed - Jan 2011
- Structure Type:
- Sewage / Water Treatment Plant
References
- Architect:
- CDM Smith
Scope Of Work
The Southeast Water Purification Plant Phase I 80 MGD expansion completed in 2011 was the largest city of Houston project undertaken, at $168 million. The capacity expansion was needed not only to increase the water available to the 1.4 million customers in the southeastern portion of Houston and seven adjacent municipalities, but to also satisfy a deadline-driven subsidence district mandate to reduce groundwater use. Teamwork, coordination, the “unexpected” and innovations were trademarks of this most successful project spanning three years, hurricanes (even snow days in Houston!), and 14 acres.
And it involved 11 stakeholder groups (nearby municipalities, water districts and other cities).
Treatment Module Two included the construction of four new flocculation and sediment basins, seven new filters, blower systems, high service sump station 2,750 horsepower split-case pump and variable frequency drive, transfer and backwash waste pump stations, chemical storage, chemical treatment facilities; installation of an upgraded SCADA system and site security system and main plant entrance; electrical and instrumentation; 2,100 LF of 96” waterlines; a new 13.4 million gallon precast ground storage tank; two new 100 ft. diameter thickeners; and new sample pump buildings; and modifications to two existing lift stations and the chlorine system. The project was completed ahead of schedule and with $200,000 savings to the owner.
Partnering
In anticipation of this project, the team initiated meetings with potential project partners. This extended project team among construction firms, engineers, sub-consultants, speciality contractors and the pertinent City department personnel participated in team-building exercises early-on, before any dirt was turned; and met quarterly to identify potential obstacles and discuss remedies. This world-class team proved itself by turning in the project months ahead of schedule!
Innovations
Early on the project team decided to use a new approach to acquiring equipment. No “just-in-time” method of logistics would suffice. Due to ample storage onsite and an extensive schedule, long lead items were released for fabrication early in the project. City personnel allowed a temporary warehouse facility to be erected onsite equipped with power and rack shelving which the project team used as a warehouse. The project team also used a field onsite for storage of items which could be exposed to the weather.
Quality construction
The project received the Associated Builders and Contractors Certificate of Merit for Excellence in Construction in 2011.
Project Challenges
The major challenge of constructing a plant of this magnitude was to effectively commission all equipment and instrumentation devices. This required a 9-month coordinated effort during which more than 200 pieces of equipment were checked individually and as part of process system. The sub-consultants and vendors working with our team went above and beyond to aid in trouble-shooting and ensured the plant functioned as intended. The team’s start-up coordinator scheduled and coordinated the delivery and receipt of 26 tank loads of treatment chemicals amounting to more than 155,000 Gallons during the three weeks prior to the final acceptance test.
During the three-year schedule many opportunities arose for inclement weather to hamper construction. Tropical Storm Edouard, Hurricane Ike, and several snow days! Despite Mother Nature’s best attempts to delay construction, through the project team’s smooth coordination, this time lost was recouped later in the schedule. This was done by testing equipment without the presence of water. Another critical factor was ensuring plant shut-down’s occurred during the low demand season or during off-peak hours. By working closely with the City’s Department of Water Operations, we ensured the project team’s work was carried out in an efficient manner without creating any instances when the plant was unable to meet its customers’ demands.
On the 3rd of February 2011, Treatment Train Two came online and began delivering water to the citizens of Houston. Following a 30-day acceptance period, the plant was awarded substantial completion, a full two months ahead of schedule.